K Swap First Start
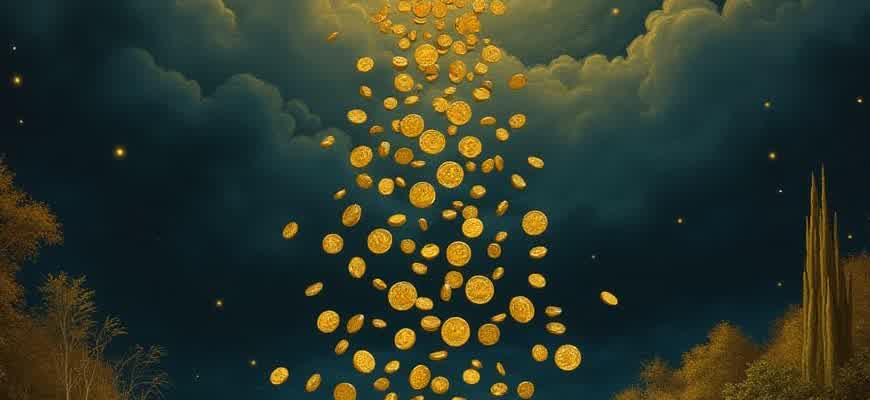
Performing the initial start after completing a K-series engine swap requires careful attention to multiple aspects to ensure the engine runs smoothly. Whether you are swapping into a Honda chassis or another platform, understanding the key steps will help you troubleshoot any potential issues effectively.
Here are the initial checks you need to perform:
- Wiring Harness: Verify that all connections are secure, and the ECU is properly wired to the engine’s sensors and components.
- Fuel System: Ensure the fuel pump is functioning and there are no leaks in the fuel lines.
- Cooling System: Confirm that the radiator and all associated hoses are properly connected and free from leaks.
- Battery: Double-check the battery connections and charge level.
Once you’ve confirmed that all systems are ready, it's time to turn the key for the first start.
Important: Before cranking the engine, ensure that there is enough oil in the engine and that the timing is set correctly. Any misfire or irregular behavior could indicate an issue with these crucial components.
If everything checks out, proceed with starting the engine. Keep an eye on the following:
- Listen for any unusual noises or irregular engine sounds.
- Monitor the temperature gauge to ensure the engine isn't overheating.
- Check for any fuel, oil, or coolant leaks.
Component | Check |
---|---|
ECU | Verify proper connection to wiring harness |
Fuel System | Test fuel pressure and check for leaks |
Cooling System | Ensure radiator is filled and there are no leaks |
Wiring Connections Check Before Starting the Engine
Before attempting to start your K Swap engine for the first time, it is critical to ensure that all electrical connections are secure and properly configured. A faulty or improperly connected wire can lead to serious issues, including engine failure, electrical short circuits, or even fire hazards. This is especially important in a swap situation, where wiring may not be standard or may require adaptation to fit the new engine. A careful inspection can save you time, money, and avoid potential damage.
When checking the wiring, focus on common problem areas such as power and ground connections, sensor wiring, and any custom or modified circuits. Following a detailed checklist will help you identify any loose, misrouted, or damaged wires. Here’s a step-by-step guide to follow before attempting to power up the engine.
Key Areas to Inspect
- Power Supply Connections – Ensure the main power wires from the battery to the engine control unit (ECU) are securely connected.
- Grounding Points – Check that all ground cables are properly attached to both the engine and chassis to avoid poor engine performance or starting issues.
- Sensor Connections – Verify that all necessary sensors (TPS, MAP, IAT, etc.) are wired correctly and functioning.
- Ignition System Wiring – Inspect all wires leading to the ignition coils and spark plugs for proper connections and no signs of wear or damage.
Steps for Checking Wiring
- Start with the Battery – Ensure the battery terminals are clean, tight, and free of corrosion.
- Verify ECU Wiring – Double-check that the ECU harness is correctly installed and there are no exposed or frayed wires.
- Inspect Grounding – Ensure all engine and chassis grounds are securely connected to minimize electrical interference.
- Check for Faulty Wires – Look for any visible damage such as cuts, abrasions, or frayed wires that could cause short circuits.
- Test Sensor Signals – Use a multimeter to check if the sensors are receiving the proper voltage and ground signals.
Important: Always ensure that power is disconnected before inspecting or adjusting any wiring to prevent electrical shock or accidental short circuits.
Common Wiring Issues to Watch For
Issue | Potential Problem |
---|---|
Loose Ground Connections | Can cause intermittent electrical issues or engine misfires. |
Incorrect Sensor Wiring | May cause inaccurate readings, leading to poor engine performance or failure to start. |
Frayed or Exposed Wires | Could lead to short circuits or fire hazards. |
Ensuring Proper Fuel Delivery After a K Swap
When swapping a K-series engine into a different chassis, ensuring that fuel is delivered properly to the new engine setup is critical. Since the K-series engines come with specific fuel requirements, it’s essential to adapt the fuel system to match the increased demands of the engine. Proper fuel delivery affects engine performance, reliability, and longevity. In this article, we'll look at key steps to ensure proper fuel flow after the swap.
Several factors need to be considered, including fuel pressure, injector size, and pump capacity. Without addressing these points, you may face issues like lean conditions, stalling, or even engine failure. Below is a breakdown of what needs to be done to ensure the fuel system is up to the task.
Key Steps for Proper Fuel Delivery
- Fuel Pump Capacity: Upgrade the fuel pump to one that can handle the increased flow rate required by the K-series engine. Consider using a high-flow fuel pump rated for your engine’s power goals.
- Fuel Injectors: Ensure you’re using injectors sized appropriately for the engine's fuel needs. Larger injectors may be necessary if the engine is turbocharged or making significant power.
- Fuel Pressure Regulator: Set the fuel pressure regulator to the correct level for the K-series engine. This may differ from the stock settings, depending on the chassis and modifications.
Common Issues to Address
- Inadequate Fuel Flow: Ensure the fuel lines are large enough to deliver sufficient fuel to the engine. Stock lines might be too small for higher-flow setups.
- Fuel Filter: Replace the stock fuel filter with one that can handle higher flow rates. A clogged or restrictive filter can starve the engine of fuel, leading to performance issues.
- Wiring and Sensors: Verify that all wiring for the fuel system, including the fuel pump and injectors, is properly integrated into the new setup. Incorrect wiring can cause intermittent fuel delivery issues.
Tip: Always double-check the fuel system components, as issues here can cause damage to your engine or even result in dangerous situations like fires or fuel leaks.
Fuel System Configuration Table
Component | Recommended Specifications |
---|---|
Fuel Pump | High-flow, rated for 300-400 LPH |
Fuel Injectors | 450-1000 cc/min, depending on power goals |
Fuel Pressure Regulator | Set to 50-60 psi for K-series engines |
Fuel Lines | AN-6 or AN-8 for high-flow applications |
What to Listen for During the First Start of Your K-Swap
Starting up your K-swapped engine for the first time is an exciting, yet crucial moment in the build process. The first start serves as an initial check to ensure all components are functioning properly and that the engine is running smoothly. It’s important to pay close attention to any abnormal sounds or irregularities, as these could signal underlying issues that need to be addressed before the engine is fully operational. Understanding what noises to expect and what might indicate a problem can save you time and money in the long run.
Here’s a breakdown of what you should listen for during the first start of your K-swap. Being able to distinguish between normal and abnormal sounds will help you identify potential issues early. Additionally, checking for any unusual noises and vibrations allows you to make necessary adjustments before putting the car into regular use.
Normal Sounds
- Starter Motor Engagement: A brief but solid cranking sound is typical as the starter motor engages.
- Idle Noise: The engine should idle smoothly. Any rough or inconsistent idling might indicate issues with the fuel system or air intake.
- Exhaust Sound: The exhaust should produce a clean, steady note. Any rattling or popping sounds could point to exhaust leaks or misfiring issues.
Unusual Noises to Watch Out For
- Engine Knock: A knocking or tapping sound, especially at higher RPMs, could indicate issues with the valvetrain or incorrect timing.
- Whining Noise: A high-pitched whining noise might be the result of a failing alternator or a misaligned accessory belt.
- Backfiring: A popping sound from the exhaust during startup may indicate issues with the ignition timing or fuel-air mixture.
What to Check if You Hear These Sounds
Pay attention to any loud or persistent noises, especially during the first few minutes of the engine running. If any unusual sounds persist, consider revisiting the installation to check for improper connections, loose bolts, or misaligned components.
Important Notes
Sound | Possible Cause | Action |
---|---|---|
Knocking | Incorrect timing, low oil pressure, or valve issues | Check oil levels, review timing settings |
Whining | Accessory belt issue or faulty alternator | Inspect belts and alternator connections |
Backfiring | Ignition or fuel delivery problem | Check spark plugs, fuel injectors, and timing |
How to Solve Common Issues During the First Start of a K Swap
Starting your K Swap for the first time can be a challenging experience, especially when you encounter unexpected issues. From electrical malfunctions to fuel delivery problems, there are several common factors to address. Early troubleshooting can save you time and ensure that your swap project is a success.
In this guide, we will cover some frequent issues and their solutions to help you quickly identify and resolve any problems that may arise during the first start of your K Swap. Properly diagnosing the issue and addressing it methodically is key to ensuring a smooth startup.
Common Problems and Solutions
- Electrical Issues: Many first start problems are related to the wiring harness or ECU connections. Incorrectly wired components can cause starting failures or improper engine behavior.
- Fuel Supply: If the fuel system isn't primed properly or the fuel pump isn't delivering the right pressure, the engine won’t start.
- Ignition Timing: If the ignition system isn’t correctly set, the engine may not fire, or it might run poorly once it starts.
Steps to Fix Common K Swap Start Problems
- Check all Wiring Connections: Ensure that the ECU is properly connected and grounded. Check the power supply to the fuel pump and ignition system.
- Verify Fuel Pressure: Using a fuel pressure gauge, check that the pressure is within the specified range for your engine. Replace or adjust the fuel pump if necessary.
- Adjust Ignition Timing: If the engine cranks but doesn’t start, verify the ignition timing with a timing light. It might need to be adjusted to match the engine’s specifications.
- Test the Starter Motor: Sometimes, the starter motor or its relay could be faulty, which prevents the engine from cranking properly. Replace or repair as necessary.
Key Troubleshooting Tips
Start by eliminating the most common causes first, such as fuel supply and electrical connections, before diving into more complex issues like ECU tuning or mechanical problems.
Table: Typical K Swap First Start Troubleshooting Checklist
Issue | Possible Cause | Solution |
---|---|---|
Engine Cranks, But Doesn't Start | Fuel pressure is too low or ignition timing is incorrect. | Check fuel pressure and verify ignition timing. |
No Crank, No Start | Starter motor failure or wiring issue. | Test starter motor, check wiring and connections. |
Erratic Idle | Vacuum leaks or incorrect tuning. | Inspect intake and vacuum lines, adjust ECU parameters. |
Post-Start Inspections: Ensuring Long-Term Engine Durability After K Swap
Once your K-series engine swap is complete and the engine has successfully started, it's crucial to perform a series of checks to confirm that everything is functioning optimally. The first few moments after the initial start are critical in assessing the overall health of your engine and preventing any long-term damage. Paying attention to these checks will help guarantee a smooth performance as you continue driving and ensuring longevity of the engine.
By closely monitoring certain aspects of the engine, you can identify any potential issues before they develop into costly repairs. From fluid levels to electrical connections, each component plays a role in the engine's performance and reliability. These preliminary checks provide a foundation for further maintenance and give peace of mind after the swap process.
Key Areas to Inspect After K-Series Engine Start
- Fluid Levels and Leaks: Ensure all fluids, including oil, coolant, and transmission fluid, are at proper levels. Check for leaks that may have developed during installation.
- Electrical Connections: Confirm that all wiring, especially ground and power connections, are secure and free of shorts.
- Engine Temperature: Monitor the engine’s temperature closely during the first few minutes of running to ensure it reaches the optimal range without overheating.
- Exhaust System: Look for unusual exhaust emissions or smells, which could indicate incomplete combustion or sensor malfunctions.
Important Post-Start Check Procedures
- Check for Unusual Noises: Listen for abnormal sounds such as knocking, ticking, or rattling, which could indicate internal issues.
- Test Idle Stability: Ensure the engine idles smoothly and does not stall or fluctuate erratically.
- Inspect for Vibration: Excessive vibration could point to issues with engine mounts, driveshaft alignment, or other components.
Ensure all electrical and mechanical components are thoroughly checked post-start to prevent future issues and maintain engine reliability.
Recommended Checks After Initial Running
Component | Check |
---|---|
Oil | Verify oil pressure and check for any leaks around seals and gaskets. |
Coolant | Monitor the coolant temperature and ensure there are no coolant leaks. |
Fuel System | Inspect fuel lines and pressure, ensuring no leaks or irregularities. |
Transmission | Test the clutch, gear shifts, and ensure smooth operation. |
By following these inspection steps immediately after starting the engine, you can prevent minor issues from becoming major problems and ensure the longevity of your K-series engine in the long run.